Getting to know instrumentation Introduction
First of all, we must first know what equipment is called precision instrument equipment. In various industries, including oil and gas industries, chemical industries, power generation and industrial automation, it is necessary to measure, control and monitor various physical parameters with very high accuracy and without errors; For this reason, we use special tools and equipment, which are called precision instruments.
In this article, we will review some common precision instruments and their applications. be with us!
Physical parameters
Physical parameters that are measured using instrumentation equipment include temperature, pressure, flow, and surface difference, which are of great importance in various industries. These parameters directly or indirectly affect the performance and quality of industrial processes. For example, measuring temperature and pressure in pressure vessels, etc. is very basic, and instrumentation equipment is used to accurately measure these parameters.
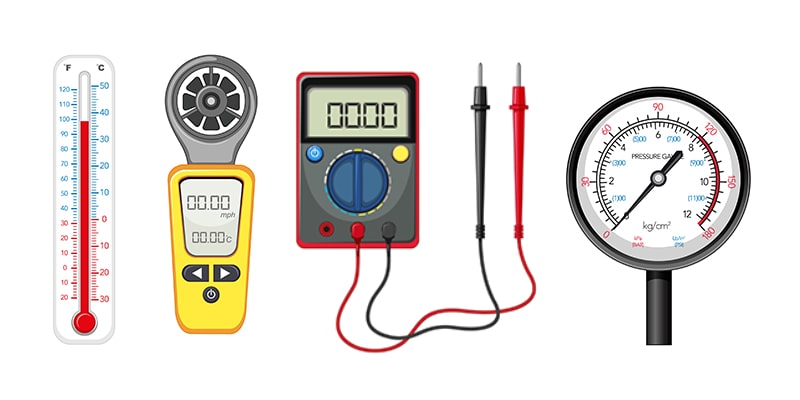
transmitter
Transmitters are equipment that convert physical parameters such as pressure, temperature, current, etc. into electrical signals. This instrumentation is very important; Because accurate measurement of these parameters is very vital to control processes and operator decisions or control system. Typically, transmitters use sensors that directly measure a physical parameter, converting the information into an electrical signal that is then transmitted to control systems or displays.
Transmitters have different types according to their application:
Pressure transmitter:
A pressure transmitter is a measuring device that is used to convert the pressure in an environment into an electrical or electronic output signal. These transmitters are used in different architectures and control systems and are usually used to measure pressure in industrial processes. These equipments can measure pressure in different ranges from low pressures to very high pressures and provide high accuracy in pressure measurement.
Pressure transmitters usually include a pressure sensor, a signal processing and amplification unit, and an electronic output unit. The pressure sensor acts as the main element of these transmitters and converts the pressure into an electrical or electronic signal. The output signal of these transmitters is usually in the form of voltage or electric current, which may be adjusted in different ways according to the type of transmitter and system requirements.
In addition to pressure measurement, pressure transmitters can have features such as high accuracy, stability over time, resistance to different environmental conditions, ability to be calibrated and connected to different control systems. These characteristics have turned them into vital tools for controlling and monitoring various industrial processes, including in oil and gas industries, chemical industries, power generation, etc.
Temperature transmitter:
The temperature transmitter is used to measure the temperature in different environments. These transmitters are among the important and vital equipment in all kinds of industries, including oil and gas industries, chemical industries, food industries, automotive industries, etc.
Temperature transmitters typically include a temperature sensor, a signal processing and amplification unit, and an electronic or electrical output unit. The temperature sensor performs the main function of these transmitters and measures the temperature in the desired environment.
By measuring the temperature and converting it into an electronic signal, temperature transmitters allow users to directly observe and control the ambient temperature. Also, these transmitters are usually offered to users with features such as high accuracy, stability over time, resistance to various environmental conditions, and the ability to connect to various control systems.
There are two different types of temperature transmitters, RTD temperature transmitters or thermocouple temperature transmitters. These transmitters use temperature sensors such as resistance sensors or thermocouples to measure temperature, and their output signal is a current signal of 4-20 mA that is transmitted to control systems or displays. These transmitters are used to measure temperature in environments with different environmental conditions (dangerous/safe) and with high accuracy.
Current transmitter:
A current transmitter is a type of instrumentation used to convert an electrical current passing through a medium into an electrical or electronic output signal. This transmitter is used as a tool to measure current in electrical and electronic circuits and systems.
Current transmitters usually include a current sensor, a signal processing and amplification unit, and an electronic output unit. The current sensor acts as the main element of these transmitters and converts the electric current into an electrical or electronic signal. The output signal of these transmitters is usually in the form of voltage or electric current, which may be adjusted in different ways according to the type of transmitter and system requirements.
Current transmitters are designed with high accuracy and stability over time and are usually used to measure current in electrical and electronic circuits and systems, including in electronic industries, automotive industries, power generation, etc. This transmitter is considered as a vital tool for controlling and monitoring current in various types of electrical circuits and systems.
Level Transmitter:
Level transmitters are commonly used to measure the level of liquids and solids in tanks. These transmitters use different sensors such as pressure difference sensor, radar, capacitive ultrasonic and displacer that can detect changes in liquid level.
The output signal of these transmitters is usually in the form of a standard signal such as 4-20 mA or 0-10 V, which is sent to control systems or displays. Level transmitters are used in various industries such as oil and gas industries, chemical industries, water and sewage industries, etc. to control and monitor various tanks.
A level transmitter usually consists of a level sensor, a signal processing and amplification unit, and an electronic or electrical output unit. The level sensor performs the main function of these transmitters and measures the liquid level in the desired environment.
The important features of level transmitters include high accuracy, stability over time, resistance to different environmental conditions, ability to be calibrated, and the possibility of connecting to different control systems and displays.
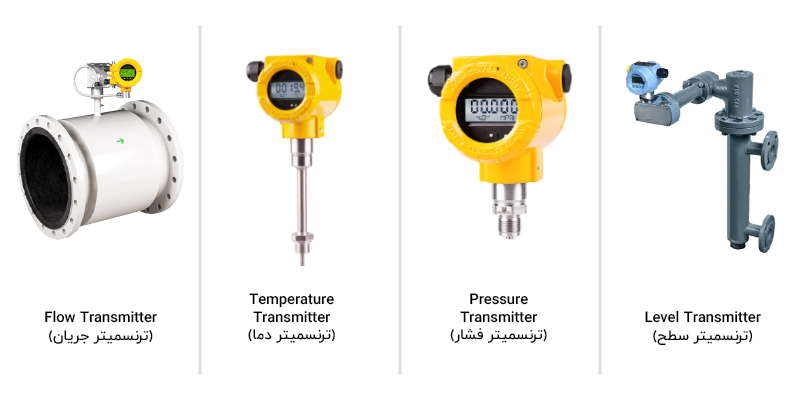
Gauge
Gauges act as direct measurement tools of physical parameters such as pressure, temperature, level, etc. These equipments directly measure the physical parameters and display the information.
Among the types of gauges, we can mention pressure gauge, temperature gauge, and level gauge, each of which is used to measure certain parameters.
Gauges in the category of instrumentation equipment are usually used as one of the important tools in various industries, including oil and gas industries, automobile manufacturing, chemical industries, electronic industries, etc. They are used to measure pressure in tanks, pipes, and various devices and play an important role in controlling and monitoring industrial processes.
pressure gauge:
Pressure gauges are used to measure pressure in different environmental conditions and in different industries, including automotive industries, petrochemical industries, etc.
An example of a pressure gauge is the Bourdon pressure gauge. These gauges use a C-shaped tube to measure pressure and display the measured information mechanically.
Temperature gauge:
Temperature gauges are used with high accuracy and in different environmental conditions to measure temperature in various industries, including electronic industries, food industries, etc.
An example of a temperature gauge is a resistance gauge. In these gauges, they use 2 non-homogeneous metals stuck together to measure temperature and display the measured information locally.
Level Gauge:
Level gauges are also used to measure the liquid level in tanks, but typically indicate the fluid level. These gauges usually have various tools that allow the user to check the liquid level more precisely (such as some output signals that can be optionally provided).
It is worth mentioning that in addition to using the level transmitter (Level Transmitter: LT), level gauges are also installed, which have the task of checking and validating the level transmitters.
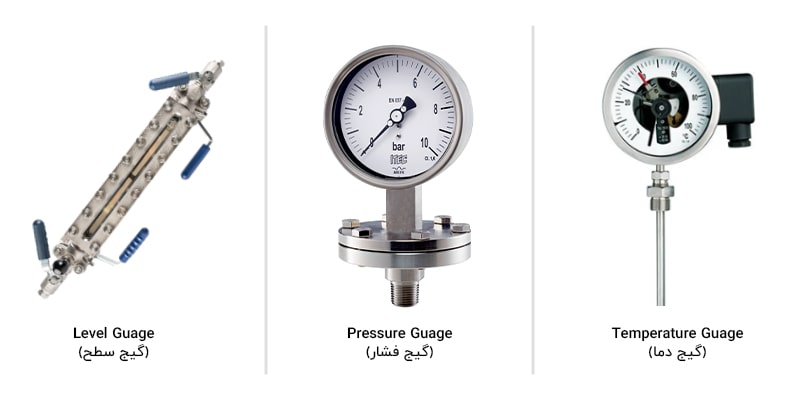
Switch
A switch is an electronic device or component that is used to control and manage the flow of electricity or electrical signals. These devices usually have one input and one or more outputs and perform a specific task that can be automatic or manual. Switches are equipment that automatically change the operation of the equipment. These equipment usually operate based on specific values of physical parameters such as pressure, temperature, etc. For example, a pressure switch can perform a specific operation such as turning a device on or off when the pressure reaches a specified minimum or maximum.
Pressure switch:
Point pressure switches are used to control various processes, including tank pressure control, pipe pressure control, or process systems, etc. An example of a pressure switch is a point pressure switch. These switches operate based on the pressure of their surroundings and open or close when the pressure reaches a certain value.
Temperature switch:
Thermal switches are used for temperature control in various types of devices and systems, including cooling devices, heating systems, etc. An example for a temperature switch is a thermal switch. These switches operate based on the temperature of their surroundings and open or close when the temperature reaches a certain value.
Current switch:
Current switches are used to control current in various types of electrical circuits and systems, including motors, automotive devices, etc. An example of a current switch is a paddle type current switch. These switches operate based on the fluid flow around them and open or close when the flow reaches a certain value.
Level Switch:
Level switches are equipment that operate based on the liquid level in the tank. When the liquid level reaches a certain point (eg above or below a certain limit), these switches perform a certain function, such as turning a device or pump on or off. For example, in a house’s water tank, a level switch can tell the water pump if the water level has reached the minimum or maximum limit.
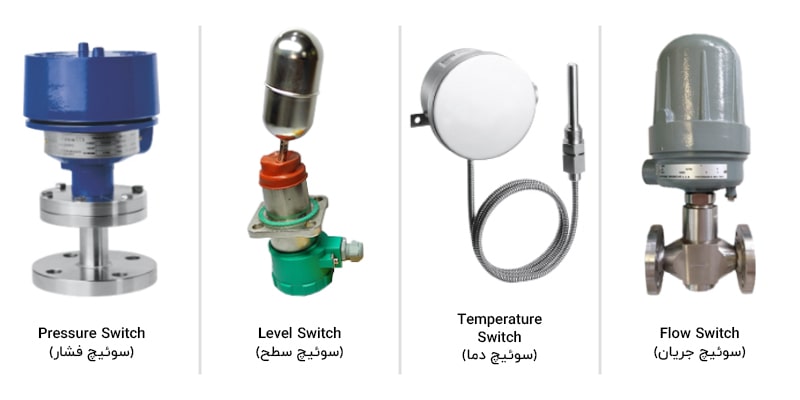
Control Valves
Among the important equipment in precision instruments are control valves or control valves that are used to control the flow of liquids or gases. These equipments accurately adjust the flow of liquids using electrical signals received from the control room or other transmitters.
Control valves are designed in different types to meet the needs of different industries, including oil and gas, chemical, water and waste water and process industries. In addition to flow control, these valves may perform other functions such as pressure, temperature, and level regulation in various systems. Control valves are widely used for accurate flow control in industrial processes and reduce wastage and optimize production processes.
Control valves consist of 3 main parts:
- Valve body: The body of control valves is usually made of carbon steel or stainless steel (S.S), which is made of resistant materials suitable for protection against fluid (pressure, temperature, wear and erosion).
- Plug: This part is placed inside the body and controls the flow of liquids by raising or lowering it.
- Operator: This part of the valve is responsible for adjusting the opening percentage and thus controlling the liquid flow. They have different types of actuators (such as a hydraulic, pneumatic or electric system) that are selected according to project limitations or project requirements.
Calibration and adjustments
Calibration is a fundamental process in the field of instrumentation equipment that is of great importance. In this process, instrumentation equipment is reviewed, re-adjusted and determined to the required accuracy using standards and special equipment. Also, the software settings are done precisely so that the measurement parameters can be adjusted with the desired accuracy. This process is done periodically and with the provision of standard conditions to ensure that the equipment works optimally and with the necessary accuracy.
Communications and connections
Communication and connections of instrumentation equipment play a very important role in collecting and transmitting measured data. These connections usually include standard communication protocols such as MODBUS, Profibus, Foundation, Hart Fieldbus, etc. Also, the use of wireless connections such as Bluetooth, Wi-Fi, etc. is also seen in some instruments. These communications are two-way and provide the possibility of transferring data to different control systems, which helps to monitor and control the processes more precisely.
Safety and standards
Compliance with safety standards and regulations for precision instrument equipment is very important. There are different standards for each type of instrumentation equipment that must be carefully followed to ensure that the equipment functions correctly and accurately, as well as to reduce the potential risks of accidents. In addition, for certain sectors of industries, there are standards such as IEC 61508 for safety equipment and IEC 61511 for process control, etc., which determine safety criteria for equipment.
Maintenance
Maintenance and repairs of precision instruments are an important part of the life cycle of these equipments. This process includes activities such as periodic review, replacement of worn parts, recalibration, etc. To ensure the optimal and stable performance of the equipment, maintenance and repairs must be performed periodically and using the instructions of the equipment manufacturer.
Also, in case of errors or problems, immediate repairs should be done to reduce the delay in the production process or avoid possible risks such as shutting down a section or the entire site.